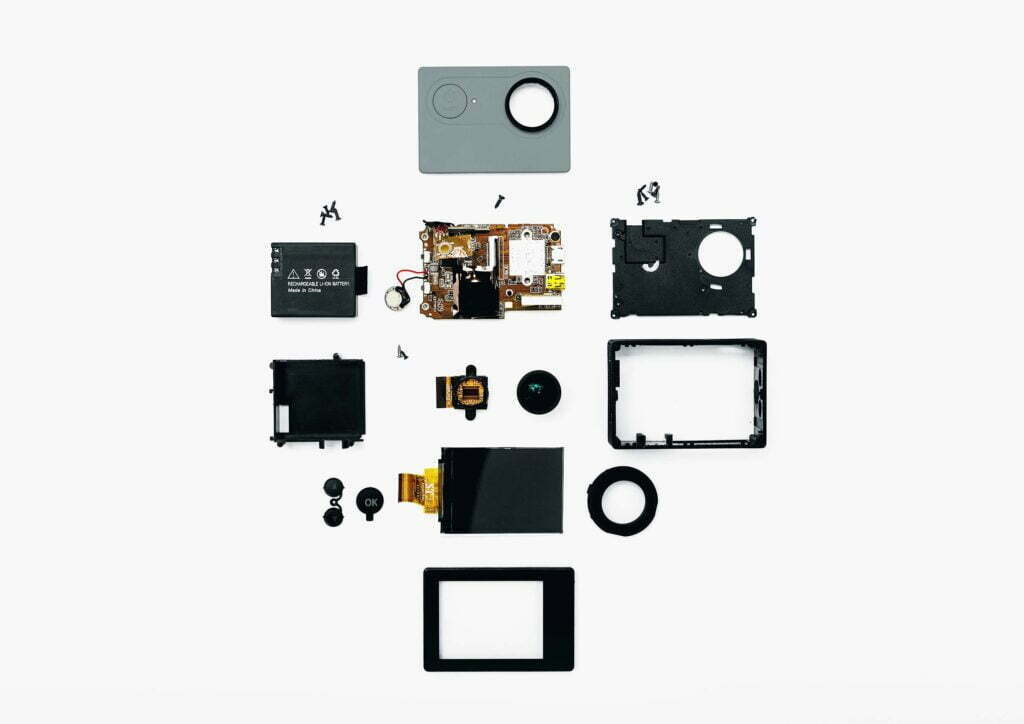
Photo by Alexander Andrews
What is Electronic Product Design?
Electronic Product Design turns a product concept into a manufacturable product that suits the market requirements. The product design goes through various processes that validates the concept through prototype development and eventually producing a cost sensitive design suitable for mass manufacturing. The important aspects of product design are,
1. New Product Introduction (NPI)
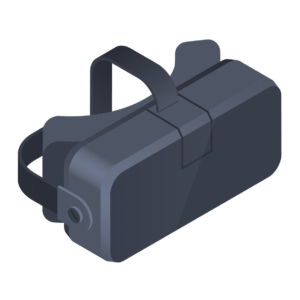
New Product Introduction encompasses all the activities required to turn a concept into a real product. There will be usually a new technology or a use-case involved. The adoption of a new technology can be unpredictable without an extensive study of the market requirements and trends. If a product concept is deemed as a breakthrough and there is much interest for it, then it can be made to a sellable product form. Creating a prototype and demonstrating the product is a crucial process in this stage. Prototypes can generate a hype around the new technology and condition the market for accepting it in the near future. Tech companies usually demonstrate their new product concepts in tech events.
2. Prototyping
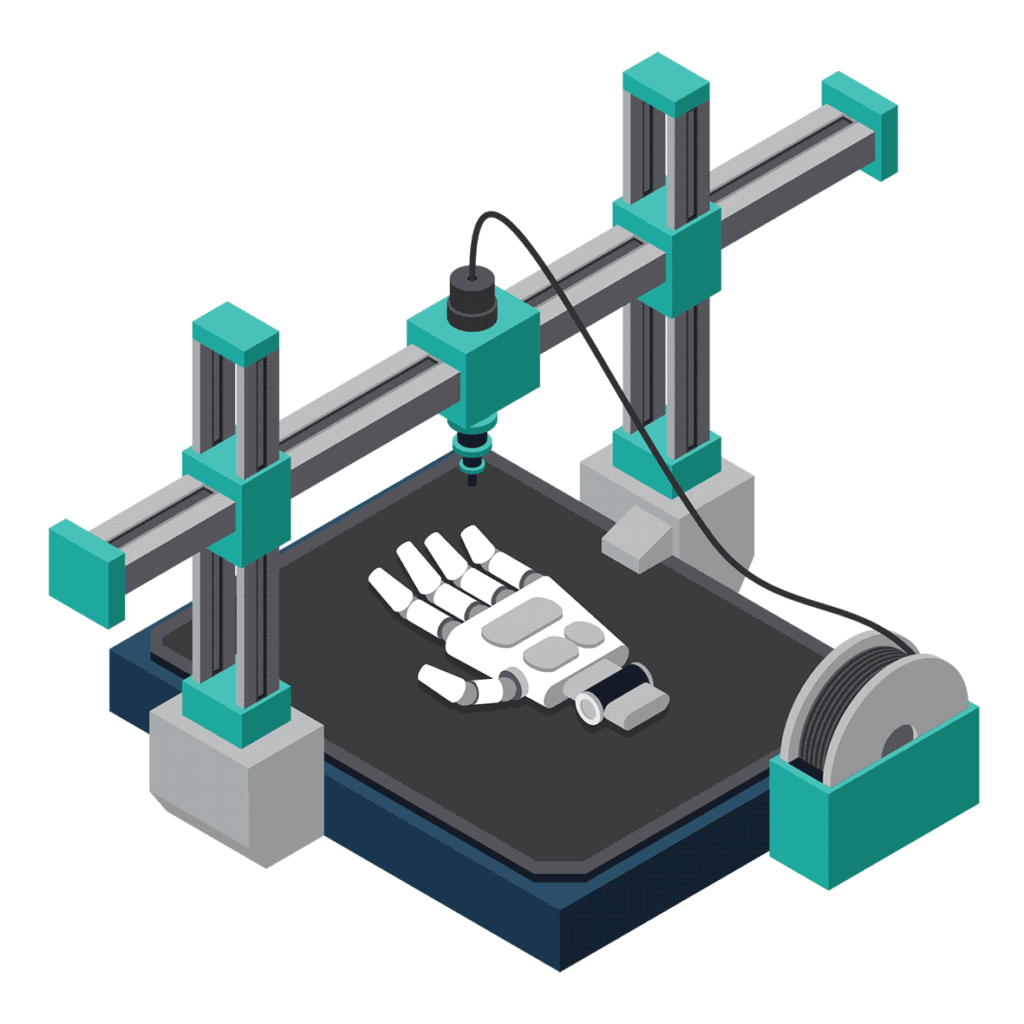
Every idea has to be tested and verified before it can be conceptualized as a product. This can be done through making a Proof-of-Concept (PoC) or a Prototype. Every feature has to be tested individually for their expected performance for the particular use case. Designs may be pushed to their extreme limits to to identify failure or pain points. The test data could then be used to identify all feasible features that could be practically implemented and transformed into manufacturable ones. Optimizations are less of a concern at prototyping stage. The priority is given to getting the idea working. Optimizations in terms of features, size and cost are done at a later stage, during pre-production design.
3. Product Life-cycle Management
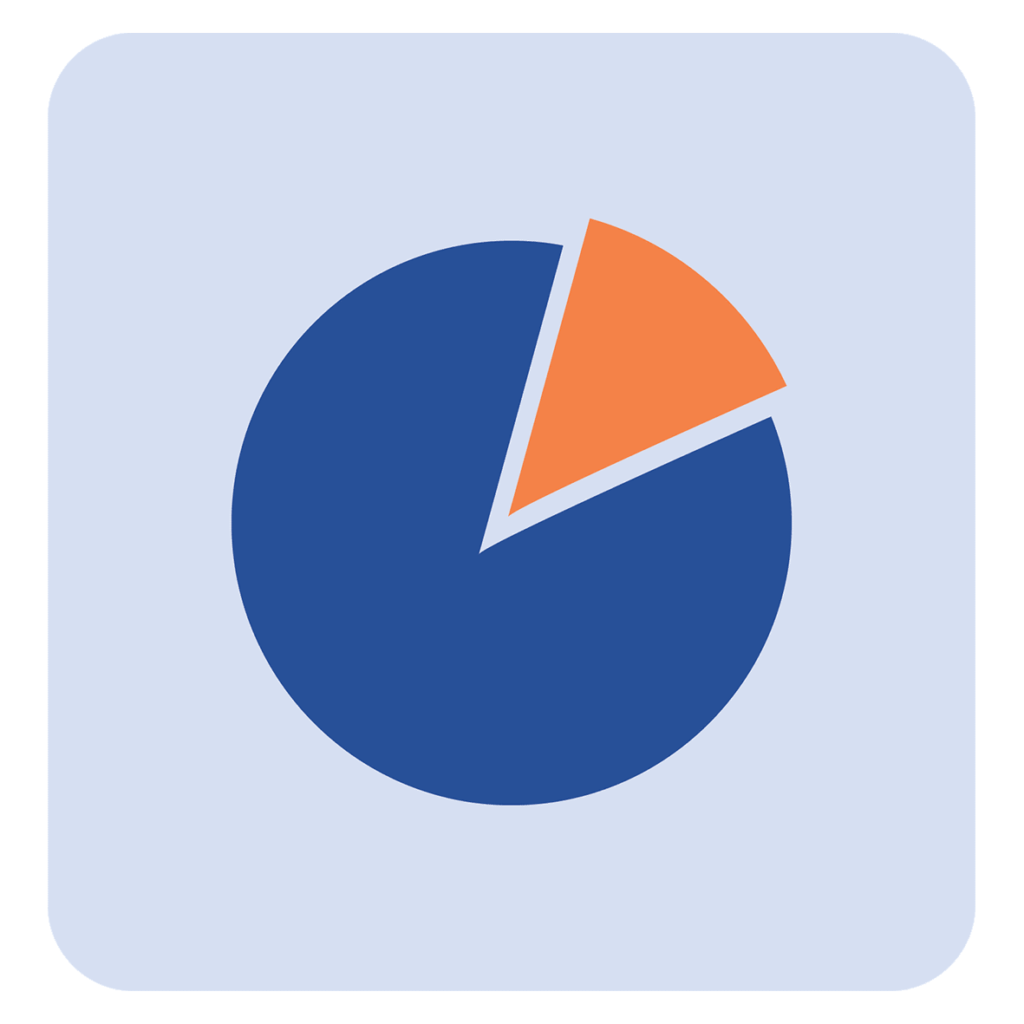
All the various stages of product development need a precise and time bounded plan before anything can take place. Managing resources such as equipments, technical expertise and data are extremely important to prevent wastage of resources. The right resources have to be timely delivered to the right processes to maintain progress. Each stage of product development should asses and validate the quality requirements for the final product. Once the product is completed and entered into production, the manufacturing process has to be carried out smoothly without any hiccups. All these processes is together called the Product Life-cycle Management.
4. Design for Manufacturing (DFM) and Design for Assembly (DFA)
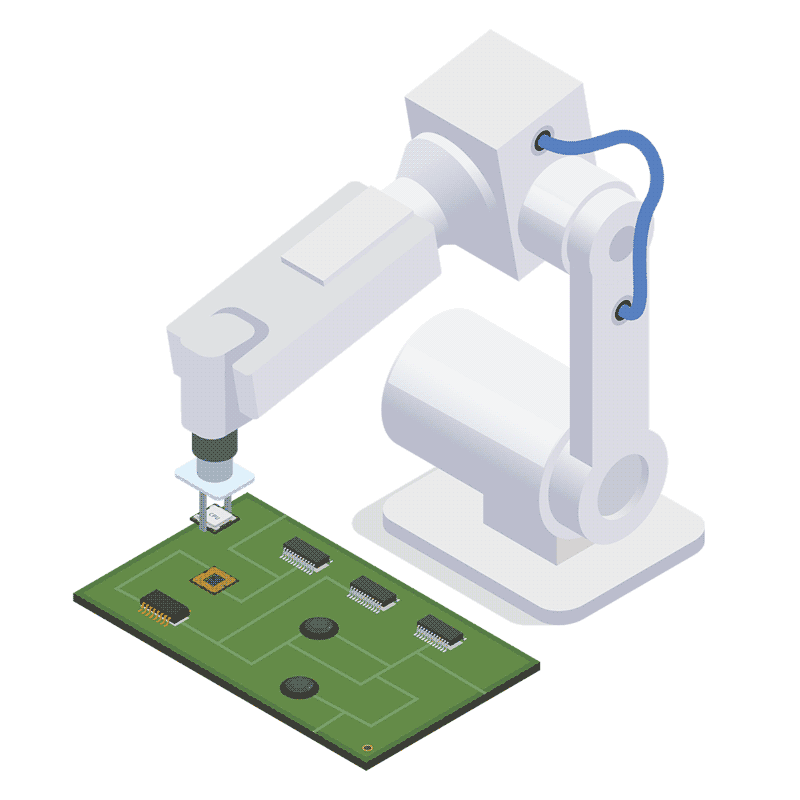
A tested product design may not be yet suitable for mass production. Automating the manufacturing process has many advantages such as reducing labor cost, lead time and production errors. Automating production requires various optimizations in the design. This optimization process is called Design for Manufacturing (DFM). A product may have multiple components that are manufactured individually. These individual components are then brought to an assembly house where they are assembled either by machines or humans. Certain design optimizations are applied in order to make the assembly process smooth. This process is called Design for Assembly (DFA).
Tell us about your requirement
Get the most cost-optimized and efficient design from us, with quality documentation and support through various stages.
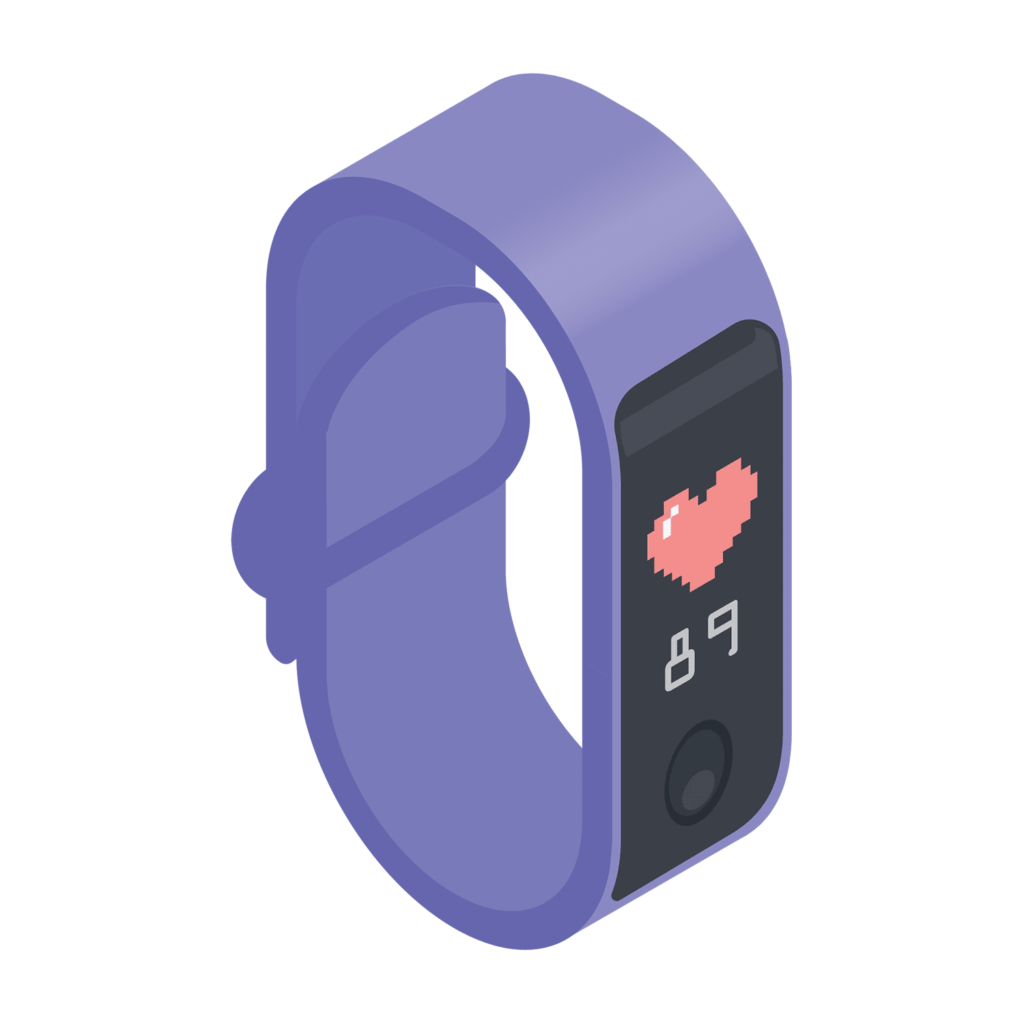